
Fuel/Solvent Recycling/Purification
Fuel/Solvent Recycling
Conventional fuel oil purification is usually done by a filter element combined with a coalescing device. The filter element usually has a pleated design to collect dirt on its surface or to trap contaminants through its depth. The coalescing device usually is made of some hydrophilic material, such as a cotton package in which micro-sized water droplets are absorbed by the highly hydrophilic cotton fibers to form a bigger water blob. The water blob is then separated from oil by a meshed Teflon screen cartridge (a separator). Often times, the processed fuel quality from conventional technology does not meet customer spec requirements and sometimes it fails far short due to stabilized emulsion. Fuel additives are commonly used in modern fuel to enhance engine performance. These additives are various types of surfactants, which will cause stabilized water-in-oil emulsion. The surfactant not only prevent the congregation of water droplets, but also changes the surface properties of a coalescer from hydrophilic to hydrophobic. This effect defeats the function of the coalescer that used to absorb the undissolved water in the fuel.
FSI uses membrane filtration to separate water from hydrocarbons (fuels/solvents). By taking advantage of the fact that water forms beads in hydrocarbons (due to higher surface tension of water compared to hydrocarbons), a membrane with a properly designed pore size will separate water beads. Being a barrier technology, membranes offer a simple and reliable approach for solving water contaminant issues in hydrocarbons. The Water Selective Membranes from FSI have an optimized pore size and surface properties that can resist high water breakthrough pressure to provide an exceptional water separation efficiency.
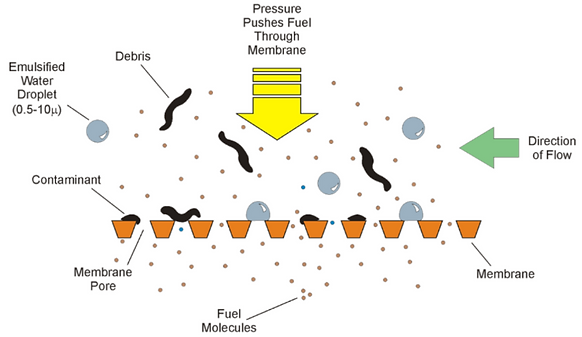.png)
Suitable Applications
-
Aviation fuels: commercial Jet A, Jet B, and Jet A-1, military JP-4, JP-5, and JP-8 with additives
-
Vehicle/commercial fuels: diesel, gasoline, and kerosene
-
Hydrocarbon solvent purification and recycling
-
Separation of emulsified water/fuel and water/solvent mixtures
-
Purification of oil refinery products

Fuel/Solvent Purification
Solids and water are contaminants commonly found in Diesel fuel. Solids may come as a result of the inherent instability of diesel fuel, the natural process of degradation, or incidental invasion during transportation, etc. Water may get into fuel systems through natural condensation, poor handling during shipping, or could simply be present in the storage tank, etc. Regardless of the source of contaminants, it is common practice to provide a fuel purification system at the point of use. Maintaining the quality of the fuel protects the capital equipment and prevents unplanned downtime in plants, both of which could be costly. Based on our fuel purification technologies developed for a Navy shipboard application as well as an Army HMMWV application, FSI has established two fuel purification product lines: FRS and FPS. With respect to the specific needs of our customers, FSI will come up with the best solution to meet fuel quality requirements using either system. Whenever helpful, our lab can test your samples or we can provide a demo unit for field testing.
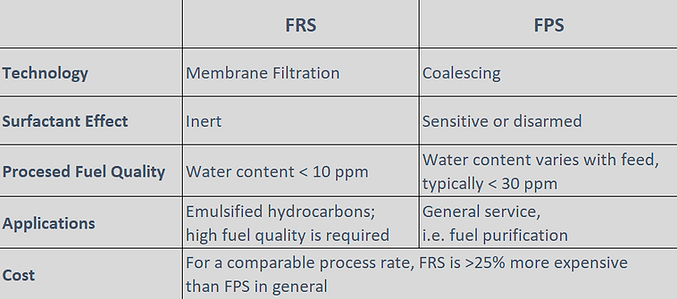.png)
.png)
.png)